Today it is popular to swap modern parts into old hot rods. One popular swap is to upgrade the factory 3 speed automatics or 3-4 speed manual to a modern 5 or 6 speed transmission with over drive. Pre 1980’s cars typically had a final drive ratio of 1:1, these transmissions had no overdrive gears, […]
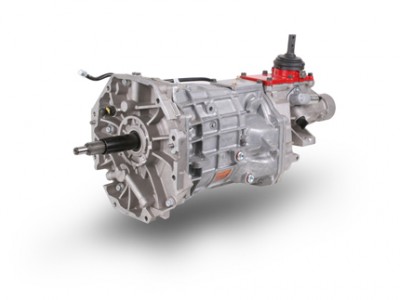