In spring of 2024 acquired a blue with black interior 2024 Acura Integra Type-S! Reliving my 2007-2014 years owning a 2007 Civic Si, I believe this car may be the pinnacle of front wheel drive sporty compact cars. Unlike the 2000 Trans Am, I can drive this car nearly anywhere anytime. Over its first year […]
2024 Acura Integra Type-S
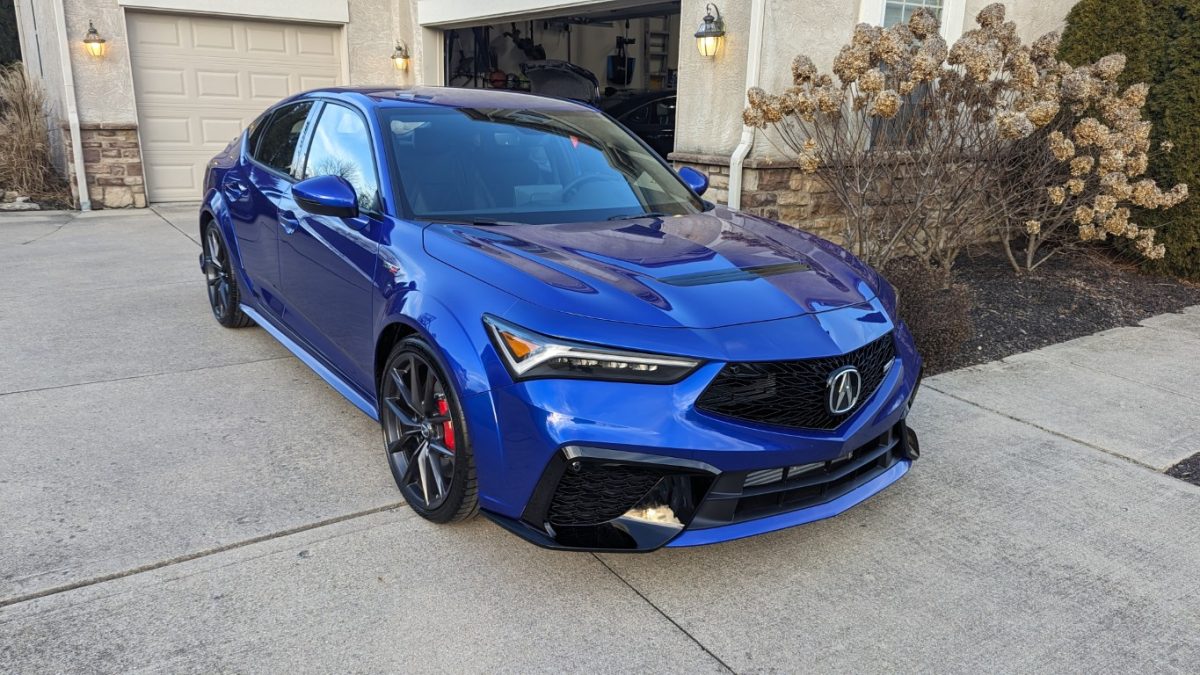